What is 5s in Manufacturing?
5s is one of the basic lean manufacturing tools we use to eliminate waste and inefficiencies out of manufacturing processes. The 5s consulting methodology consists of phases: They can be translated from the Japanese as “sort”, “set in order”, “shine”, “standardize”, and “sustain”.
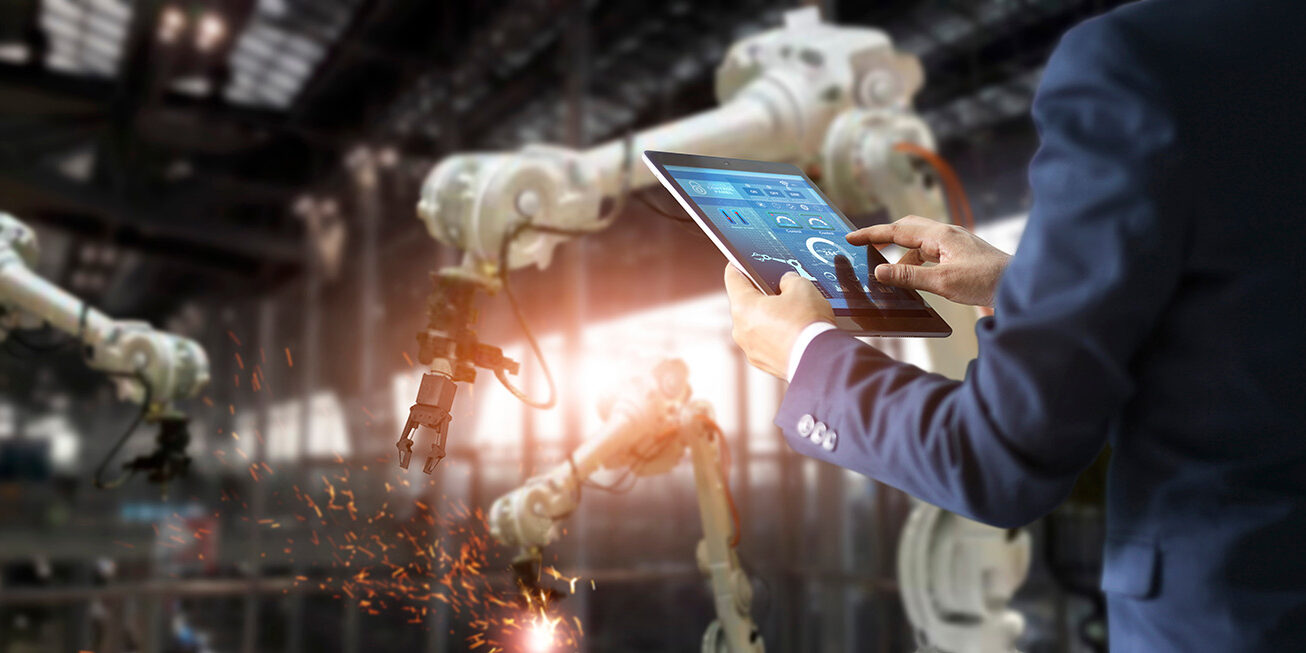
The 5s Consulting Phases
- Make work easier by eliminating obstacles
- Reduce chances of being disturbed with unnecessary items
- Evaluate necessary items with regard to cost or other factors
- Remove all parts or tools that are not in use
- Segregate unwanted material from the workplace
- Define Red-Tag area to place unnecessary items that cannot immediately be disposed of
- Need a fully skilled supervisor for checking on a regular basis
- Waste removal
- Make clear all working floor except using material
- Sort bad and good things
- Sort all items as per their parts
- Arrange all necessary items so that they can be easily selected for use
- Prevent loss and waste of time by arranging workstation in such a way that all tooling/equipment is in proximity
- Make it easy to find and pick up necessary items
- Ensure a first-in-first-out FIFO basis
- Make workflow smooth and easy
- All the above work should be done on a regular basis
- Place components according to their uses, with the frequently used components being nearest to the workplace
- Clean your workplace on daily basis completely or set cleaning frequency time to time
- Use cleaning as an inspection
- Prevent machinery and equipment deterioration
- Keep workplace safe and easy to work
- Keep the workplace clean and pleasing to work in
- When in place, anyone not familiar to the environment must be able to detect any problems within 50 feet in 5 sec
- Standardize the best practices in the work area
- Maintain high standards in workplace organization at all times
- Everything in its right place
- Every process has a standard
- Standardize color coding of usable items
- People know the process of that specific job
- Not harmful to anyone
- Also translates as “do without being told”
- Perform regular audits
- Training and discipline
- Training is a goal-oriented process
- Self-discipline
- To maintain proper order
- Ensure all defined standards are being implemented and heard
- Follow the process, but also be open to improvement
5s Consulting Methodology Benefits
The efficient implementation of the 5s technique leads to improvement in the productivity of the manufacturing plant. It promotes neatness in the storage of raw material and finished products. The 5s implementation leads to the improvement of the case company organization in many ways such as
The 5s methodology can be used in any industry to create an organized clutter-free work environment.
The TPT Difference
A 5s engagement with us begins with an initial meeting with your stakeholders at your facility. An assessment of your current state operations is important to establish the ultimate scope of work and project timeline and a financial proposal.
For more information on our 5s consulting services and our 5s Methodology consultants can help support your needs, contact the team at TPT today!
Contact Us to Learn More About 5s Consulting Services
TPT is the leading provider of 5s consulting services. Contact us today to speak with one of our planning and engineering specialists.